Best way to bolt on bolt on sliders?
#41
Registered User
Join Date: Feb 2003
Location: Mount Pleasant, SC
Posts: 993
Likes: 0
Received 0 Likes
on
0 Posts
Originally Posted by Jeff the marmot
It totally depends on the design whether weld-on or bolt-on is better. I originally had weld-on, but cracked the welds on both sides after lots of slamming them into rocks. I was also amazed at the massive amount of rust underneath all the plates since moisture got in through the holes in the frame that are there from the factory.
I agree that I wouldn't have confidence in slamming sliders if they were only held there with self-tapping screws, but I realize that Roger B. has pretty much proven that it's OK to do that despite that it doesn't look right.
I have far more confidence in the strength of my bolt-on solution since I've used much thicker steel for the brackets and it's not totally relying on the bolts either. Plus vertical welds and plates would increase the chance of cracking the frame vertically there, so I'm glad I've gotten away from that. I replaced each side of the sliders separately as I cracked them off the frame. My new bolt-on solution wraps around 3 sides of the frame, so it's much stronger, fewer disadvantages, and more advantages, compared to my weld-on solution. I explained it more at the top of the page here:
http://www.4x4wire.com/toyota/tech/sliders/
Now I just have to hope that the frame is still strong enough where it was welded since I've changed the internal "structure" of the metal where it was welded.
I agree that I wouldn't have confidence in slamming sliders if they were only held there with self-tapping screws, but I realize that Roger B. has pretty much proven that it's OK to do that despite that it doesn't look right.
I have far more confidence in the strength of my bolt-on solution since I've used much thicker steel for the brackets and it's not totally relying on the bolts either. Plus vertical welds and plates would increase the chance of cracking the frame vertically there, so I'm glad I've gotten away from that. I replaced each side of the sliders separately as I cracked them off the frame. My new bolt-on solution wraps around 3 sides of the frame, so it's much stronger, fewer disadvantages, and more advantages, compared to my weld-on solution. I explained it more at the top of the page here:
http://www.4x4wire.com/toyota/tech/sliders/
Now I just have to hope that the frame is still strong enough where it was welded since I've changed the internal "structure" of the metal where it was welded.
Dave
#42
Registered User
Join Date: May 2003
Location: Susanville, CA.
Posts: 207
Likes: 0
Received 0 Likes
on
0 Posts
[QUOTE=Nobody]Misguided is probably the word...in talking with a professional welder where i live-he states that you Never weld to a frame..something about the cooling down of the surounding metal weakens it [QUOTE]
This is simply not true concerning light duty trucks! Next time you see the professional you should ask him how they get away with making the frame a welded assembly in the first place if everywhere they(the factory) make a weld the crytal structure changes for the worst? One of the beautiful things about mild steel is its abiltiy to be welded , shaped with little or no real detrimental effects to its abilty to do the job. This in sharp contrast to other alloys of steel or other materials in general.
Now in the world of OTR-Heavy duty commercial trucks (NON light duty trucks) welding on the frames is an absolute no-no. However they use completely different grades of steel , and do not use welding in their origanal construction. If you look closely at the frames (on the rig itself) you will see a huge sticker stating not to weld on the chassis.
Anyhow I respect your desicion to mount the sliders anyway you want, and I am truly glad that it works for you & the others who have done it this way. At this point I am just trying to educate the YT board as to the truth about welding on frames. I write the facts not what some one person has told me. Amazingly enough there are many pros who dont really know what they are talking about.
I remember being on a feild job concerning a new hospital , and having a pro (an AWS inspector II ,had been one for years) telling me to do a job a certain way , and with a certain wire. I knew it was wrong , and refused to do it which of course sent this guy , and his Co. into a tail spin. I had to go through major hoops to get to people who knew the facts ,and to get inspectors above them to fix the whole sitation(a nightmare but the right thing to do). I can only imagine how many jobs this guy & Co. has made mistakes on. The job in question was concerning seismic codes (earthquake construction) , and I know that the Co. in question had done numerous projects in areas where this code is required. My point is even the pros have no clue sometimes (scary). It would be true that I learn something most everyday about something to do with this feild -however I keep my mouth shut if I do not know for sure the facts of the subject.
Hope you understand where I am coming from,
Richard S.
This is simply not true concerning light duty trucks! Next time you see the professional you should ask him how they get away with making the frame a welded assembly in the first place if everywhere they(the factory) make a weld the crytal structure changes for the worst? One of the beautiful things about mild steel is its abiltiy to be welded , shaped with little or no real detrimental effects to its abilty to do the job. This in sharp contrast to other alloys of steel or other materials in general.
Now in the world of OTR-Heavy duty commercial trucks (NON light duty trucks) welding on the frames is an absolute no-no. However they use completely different grades of steel , and do not use welding in their origanal construction. If you look closely at the frames (on the rig itself) you will see a huge sticker stating not to weld on the chassis.
Anyhow I respect your desicion to mount the sliders anyway you want, and I am truly glad that it works for you & the others who have done it this way. At this point I am just trying to educate the YT board as to the truth about welding on frames. I write the facts not what some one person has told me. Amazingly enough there are many pros who dont really know what they are talking about.
I remember being on a feild job concerning a new hospital , and having a pro (an AWS inspector II ,had been one for years) telling me to do a job a certain way , and with a certain wire. I knew it was wrong , and refused to do it which of course sent this guy , and his Co. into a tail spin. I had to go through major hoops to get to people who knew the facts ,and to get inspectors above them to fix the whole sitation(a nightmare but the right thing to do). I can only imagine how many jobs this guy & Co. has made mistakes on. The job in question was concerning seismic codes (earthquake construction) , and I know that the Co. in question had done numerous projects in areas where this code is required. My point is even the pros have no clue sometimes (scary). It would be true that I learn something most everyday about something to do with this feild -however I keep my mouth shut if I do not know for sure the facts of the subject.
Hope you understand where I am coming from,
Richard S.
#43
Registered User
Join Date: Apr 2003
Location: A stone's throw from the Rose Parade
Posts: 228
Likes: 0
Received 0 Likes
on
0 Posts
Honestly I think it's simple preference. I chose to bolt mine on so I could remove them easily. They are stronger than the trails I subject my truck to and that is the purpose. I wouldn't liken them to nerf bars but I suppose everyone has their view. I've seen people wheel with nerf bars. It's pretty funny. A friend wheeled sledgehammer with some. He had removed his doors to keep them from getting rashed. After the run the doors wouldn't fit anymore because the kick panels had two BIG dents in them.
I have also welded people's sliders to their frames for them. In some cases you have to if they are not designed for the pinch weld.
I have also welded people's sliders to their frames for them. In some cases you have to if they are not designed for the pinch weld.
#44
Contributing Member
Join Date: Aug 2002
Location: Las Vegas
Posts: 159
Likes: 0
Received 0 Likes
on
0 Posts
This is simply not true concerning light duty trucks! Next time you see the professional you should ask him how they get away with making the frame a welded assembly in the first place if everywhere they(the factory) make a weld the crytal structure changes for the worst? One of the beautiful things about mild steel is its abiltiy to be welded , shaped with little or no real detrimental effects to its abilty to do the job. This in sharp contrast to other alloys of steel or other materials in general.
Hope you understand where I am coming from,
Richard S.
Hope you understand where I am coming from,
Richard S.

I was under the impression (from the pro welder) that the frame is welded from the factory while all of it is 'hot' and allowed to cool down all at once-therefore preventing any crystalization..he does work on heavy duty trucks so it looks like he took the default position on every frame-sounds safe to me. I have never herd of welded on sliders causing a catastrophic frame failure- I think you are safe either way (bolting-bolting through or welding) depending on your application.
#45
Contributing Member
Join Date: May 2002
Location: Wandering around Phoenix
Posts: 6,033
Likes: 0
Received 3 Likes
on
3 Posts
Originally Posted by 44Runner
Self tapping bolts are well and good for people that want to look like they know what they are doing, but in reality, if you start beating on them, they are gonna pull out of the frame. Those are the facts. Welding on or sleeved is the ONLY way to go, PERIOD.
Dave
Dave
#46
Registered User
Join Date: May 2003
Location: Susanville, CA.
Posts: 207
Likes: 0
Received 0 Likes
on
0 Posts
I am going to attach a couple of pictures of my work truck a 2003 3/4 ton pickup. It's frame rails are no different than any other light duty truck/car with the simple exception that the rails are hydro formed vs. the more common (not for long) stamping or roll forming.
The reason for these pictures is to show examples of myths associated with welding on frames.
The first would be "Dont make a vertical weld on the web of the frame!" UNTRUE but most of you have heard that for years. You can clearly see vertical welds in both pictures , and one clearly shows this done on a heavily stressed member.
The second would be not welding in a horizonal plane anywhere close to , and running parallel with the bottom of the frame. Look at the transfer/transmission crossmember - Yup it was done here.
The third would be "the frame should be a countinous unit- hence not having more than one tube per complete rail length". Again NOT TRUE if you look at the C shaped weld area that is a tube meeting up with another tube, and in this truck there are three sections per side that do this!
There are tons of little things but you are by now getting the picture , and that is that you can do alot of things to a light duty truck/car frame. One thing that you dont see in these pictures is holes anywhere near the edge of the web. My point is welding is safe in the hands of a competent person.
Once again I do respect your decision to choose whatever method of attachment you prefer. I am just presenting some facts , and examples to make you all better informed.
Take care,
Richard S.
The reason for these pictures is to show examples of myths associated with welding on frames.
The first would be "Dont make a vertical weld on the web of the frame!" UNTRUE but most of you have heard that for years. You can clearly see vertical welds in both pictures , and one clearly shows this done on a heavily stressed member.
The second would be not welding in a horizonal plane anywhere close to , and running parallel with the bottom of the frame. Look at the transfer/transmission crossmember - Yup it was done here.
The third would be "the frame should be a countinous unit- hence not having more than one tube per complete rail length". Again NOT TRUE if you look at the C shaped weld area that is a tube meeting up with another tube, and in this truck there are three sections per side that do this!
There are tons of little things but you are by now getting the picture , and that is that you can do alot of things to a light duty truck/car frame. One thing that you dont see in these pictures is holes anywhere near the edge of the web. My point is welding is safe in the hands of a competent person.
Once again I do respect your decision to choose whatever method of attachment you prefer. I am just presenting some facts , and examples to make you all better informed.
Take care,
Richard S.
#47
Contributing Member
[QUOTE=weldpro]Misguided is probably the word...in talking with a professional welder where i live-he states that you Never weld to a frame..something about the cooling down of the surounding metal weakens it
This is simply not true concerning light duty trucks! Next time you see the professional you should ask him how they get away with making the frame a welded assembly in the first place if everywhere they(the factory) make a weld the crytal structure changes for the worst? One of the beautiful things about mild steel is its abiltiy to be welded , shaped with little or no real detrimental effects to its abilty to do the job. This in sharp contrast to other alloys of steel or other materials in general.
Now in the world of OTR-Heavy duty commercial trucks (NON light duty trucks) welding on the frames is an absolute no-no. However they use completely different grades of steel , and do not use welding in their origanal construction. If you look closely at the frames (on the rig itself) you will see a huge sticker stating not to weld on the chassis.
Anyhow I respect your desicion to mount the sliders anyway you want, and I am truly glad that it works for you & the others who have done it this way. At this point I am just trying to educate the YT board as to the truth about welding on frames. I write the facts not what some one person has told me. Amazingly enough there are many pros who dont really know what they are talking about.
I remember being on a feild job concerning a new hospital , and having a pro (an AWS inspector II ,had been one for years) telling me to do a job a certain way , and with a certain wire. I knew it was wrong , and refused to do it which of course sent this guy , and his Co. into a tail spin. I had to go through major hoops to get to people who knew the facts ,and to get inspectors above them to fix the whole sitation(a nightmare but the right thing to do). I can only imagine how many jobs this guy & Co. has made mistakes on. The job in question was concerning seismic codes (earthquake construction) , and I know that the Co. in question had done numerous projects in areas where this code is required. My point is even the pros have no clue sometimes (scary). It would be true that I learn something most everyday about something to do with this feild -however I keep my mouth shut if I do not know for sure the facts of the subject.
Hope you understand where I am coming from,
Richard S.
Just to add to Richard on the "welding to the frame" point. Whether or not to weld depends on what the material is you are welding. If you are welding mild steel then no problem at all especially if it shows welds from assembly. There are some cases where bolts would be better. The first would be if the frame has been hardened via heat treatment (heat treatment is why aluminum welds are so weak compared to the rest of the metal, the entire part must be re-heat treated to regain all original strength). I have yet to see a frame that has this done to it but that does not mean that they don't exist. The second is when it it hydroformed. This process actually work hardens the steel when it is injected with super high pressure water to create tons of forming pressure. Check out this link for more about it. If you do need to weld to a hardened frame make sure to use the correct filler material (either rod or wire) and try not to weld onto the top or especially not the bottom of the frame in any section from the front to the rear wheels. This will minimize the effect of the damage to the strength of the tube material by limiting it to where it sees the least stresses. Actually where Richard is welding the sliders from an engineering standpoint is perfect and exactly where the should be to minimize the effect I was talking about.
This is a basic plot of the stresses (red is highest) on a wrench (but we can approximate the frame with it as well).
See how the higher stress is on the top and bottom (in red) yet far less on the sides (in blue)?
That blue streak is where the sliders should be welded to minimally affect strength.
Sorry for the giant pic tho!
This is simply not true concerning light duty trucks! Next time you see the professional you should ask him how they get away with making the frame a welded assembly in the first place if everywhere they(the factory) make a weld the crytal structure changes for the worst? One of the beautiful things about mild steel is its abiltiy to be welded , shaped with little or no real detrimental effects to its abilty to do the job. This in sharp contrast to other alloys of steel or other materials in general.
Now in the world of OTR-Heavy duty commercial trucks (NON light duty trucks) welding on the frames is an absolute no-no. However they use completely different grades of steel , and do not use welding in their origanal construction. If you look closely at the frames (on the rig itself) you will see a huge sticker stating not to weld on the chassis.
Anyhow I respect your desicion to mount the sliders anyway you want, and I am truly glad that it works for you & the others who have done it this way. At this point I am just trying to educate the YT board as to the truth about welding on frames. I write the facts not what some one person has told me. Amazingly enough there are many pros who dont really know what they are talking about.
I remember being on a feild job concerning a new hospital , and having a pro (an AWS inspector II ,had been one for years) telling me to do a job a certain way , and with a certain wire. I knew it was wrong , and refused to do it which of course sent this guy , and his Co. into a tail spin. I had to go through major hoops to get to people who knew the facts ,and to get inspectors above them to fix the whole sitation(a nightmare but the right thing to do). I can only imagine how many jobs this guy & Co. has made mistakes on. The job in question was concerning seismic codes (earthquake construction) , and I know that the Co. in question had done numerous projects in areas where this code is required. My point is even the pros have no clue sometimes (scary). It would be true that I learn something most everyday about something to do with this feild -however I keep my mouth shut if I do not know for sure the facts of the subject.
Hope you understand where I am coming from,
Richard S.
This is a basic plot of the stresses (red is highest) on a wrench (but we can approximate the frame with it as well).

See how the higher stress is on the top and bottom (in red) yet far less on the sides (in blue)?
That blue streak is where the sliders should be welded to minimally affect strength.

Sorry for the giant pic tho!

Last edited by MTL_4runner; 03-04-2004 at 10:34 AM.
#48
Registered User
Join Date: May 2003
Location: Susanville, CA.
Posts: 207
Likes: 0
Received 0 Likes
on
0 Posts
another pic for you guys to look at.
Oh , and Roger Brown is a smart guy I know him from many years over at the Pirate board , and he is the only real reason I can accept the self tappers as I highly doubt he would make a crappy product. So for now becuase of him (RB) I will accept the self tappers as a viable method of attachment.
Richard
Oh , and Roger Brown is a smart guy I know him from many years over at the Pirate board , and he is the only real reason I can accept the self tappers as I highly doubt he would make a crappy product. So for now becuase of him (RB) I will accept the self tappers as a viable method of attachment.
Richard
#49
Registered User
Join Date: May 2003
Location: Susanville, CA.
Posts: 207
Likes: 0
Received 0 Likes
on
0 Posts
MTL- I do agree with what you are writing. It will look asthough I am going against that in a couple of statements (horizontal welding, the no concern type attitude with the hydroformed frame with tons of welding). Just remember this is a broad statement I am making , and we both know there are alot of rules that go into making it right!
Richard
Richard
#50
Contributing Member
Originally Posted by weldpro
MTL- I do agree with what you are writing. It will look asthough I am going against that in a couple of statements (horizontal welding, the no concern type attitude with the hydroformed frame with tons of welding). Just remember this is a broad statement I am making , and we both know there are alot of rules that go into making it right!
Richard
Richard

#52
Contributing Member
Join Date: May 2002
Location: Wandering around Phoenix
Posts: 6,033
Likes: 0
Received 3 Likes
on
3 Posts
Originally Posted by weldpro
So for now becuase of him (RB) I will accept the self tappers as a viable method of attachment.
Richard
Richard
#53
Registered User
Join Date: May 2003
Location: Susanville, CA.
Posts: 207
Likes: 0
Received 0 Likes
on
0 Posts
Robinhood- you are right , and that is what I was refering to. Thanks for adding that as that would have haunted me at some point I can assure you!
Richard S.
Richard S.
#55
Contributing Member
Originally Posted by Robinhood150
Well, only if the load on the sliders is transfered to the pinch weld. That way there is very little tension on the bolts. If the self tappers have to carry all the load, they will fail eventually.
Robinhood and Richard I am totally with you guys on the self tapping screws....those are meant for sheet metal and light duty assembly work only!!! From an engineering standpoint they are not at all for any type of structural intergrity. I would not trust those things as far as I could throw them, the strength on those is total crap. In that case the slider is just barely stronger that a nerf bar. Even if people are not going to do any serious wheeling, if they will use them for anything other than show they should still have sleves installed for bolting them in and should use grade 8 through bolts and nuts or better.
This picture is seriously disturbing to the engineer in me.
It may never fail but I wouldn't put my name on the design.

Last edited by MTL_4runner; 03-04-2004 at 11:27 AM.
#56
Contributing Member
Thread Starter
Join Date: Oct 2003
Location: St. Louis, MO
Posts: 537
Likes: 0
Received 0 Likes
on
0 Posts
Well, in the end, though I'd sort of decided to weld them, I went ahead and bolted them on.
The one post about my probably not bashing them to badly came to mind, and also, when I was c-clamping them to the frame to see how they looked, I realized the inner bar was directly under the pinch weld so I put them on RBrown style where they're close enough that under flex, the pinch weld will make contact with the length of the bar.
At later date, when I'm more comfortable for more challenging trails, I'm going to pull them off, and put grade 8 bolts through sleeves on the lower 6 bolts on each side.
For now, I think this is fine, however.
Several people wanted to see them on, so there you have it.
Bill
The one post about my probably not bashing them to badly came to mind, and also, when I was c-clamping them to the frame to see how they looked, I realized the inner bar was directly under the pinch weld so I put them on RBrown style where they're close enough that under flex, the pinch weld will make contact with the length of the bar.
At later date, when I'm more comfortable for more challenging trails, I'm going to pull them off, and put grade 8 bolts through sleeves on the lower 6 bolts on each side.
For now, I think this is fine, however.

Bill
#57
Contributing Member
iTrader: (3)
I've had my sliders bolted on for years, first set were only self-tapping bolts, never had a problem in the years they were like that, including a few crossings of the Rubicon:
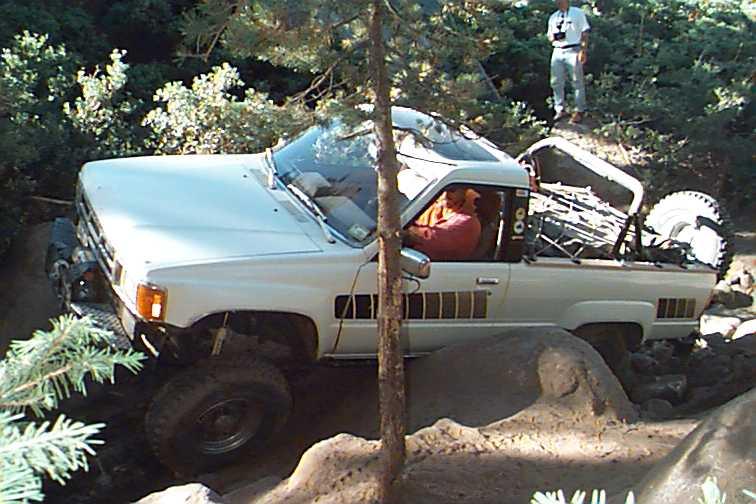
Current sliders are mounted with a combination of sleeved thru-bolts and tapped bolts. I offer my sliders in several mounting styles, and for self-tapping bolts, you can run them as-is, or drill thru the frame for a thru-bolt or have the bottom corners welded in place, or just weld them in place from the get-go:
http://www.4crawler.com/4x4/ForSale/...shtml#Mounting
BTW: My sliders utilize an inner tube the rides under the body pinch weld to transfer extreme loads to the body.
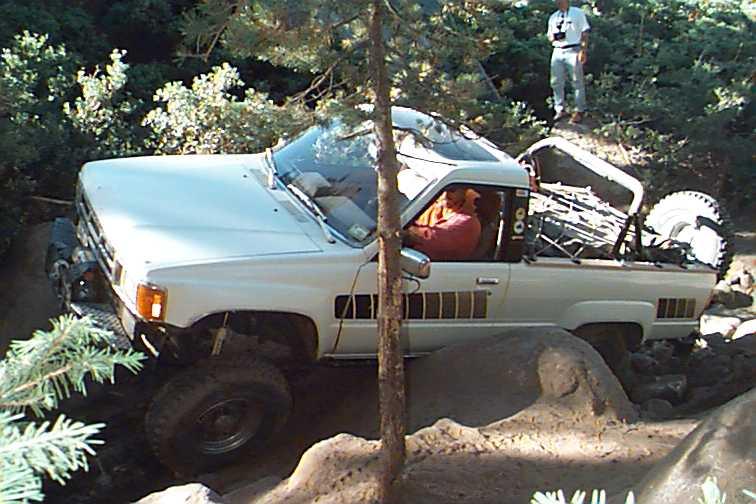
Current sliders are mounted with a combination of sleeved thru-bolts and tapped bolts. I offer my sliders in several mounting styles, and for self-tapping bolts, you can run them as-is, or drill thru the frame for a thru-bolt or have the bottom corners welded in place, or just weld them in place from the get-go:
http://www.4crawler.com/4x4/ForSale/...shtml#Mounting
BTW: My sliders utilize an inner tube the rides under the body pinch weld to transfer extreme loads to the body.
Last edited by 4Crawler; 03-21-2004 at 08:46 AM.
#59
Registered User
Join Date: Feb 2003
Location: James Island/ChuckTown, SC
Posts: 698
Likes: 0
Received 0 Likes
on
0 Posts
So if one wants to mount them with self tapping screws and to where they will contact the pinch weld under stress, how far below the weld should they be mounted?
#60
Contributing Member
iTrader: (3)
Originally Posted by ssbogger
So if one wants to mount them with self tapping screws and to where they will contact the pinch weld under stress, how far below the weld should they be mounted?
I cover that in my installation instructions:
http://www.4crawler.com/4x4/ForSale/...l#Installation