4runner home made bumper
#21
Registered User
Join Date: Apr 2010
Location: Floriduh & South Africa
Posts: 43
Likes: 0
Received 0 Likes
on
0 Posts
Try starting with something structurally safe and build from there. I am doing the exact same thing myself. Use one of these from trail gear and build off of it. It may cost a bit, but you will be money ahead in time and safety. Build off of this and even if you totally eff it up and are unhappy with it, you know it will still perform the way it was intended.
From trail gear:
Here's the one I am in the middle of building:
When it's all said and done, the solid foundation counts for EVERYTHING!
With the welder, throw away the .030 wire that came with the machine and get some Lincoln .035 wire and use it. It will fit. You may have to get .035 tips from HF. Turn the voltage setting to high, the wire speed to 7 and PRACTICE ON SOME SCRAP! You are ready when the back of whatever you are welding has an evenly distributed line of dark blue discoloration the length of your weld. Get a book on mig welding or pay a welder his shop rate for an hour to give you some "hands on" pointers. Good luck! We all have to start somewhere, just don't give up!
From trail gear:


When it's all said and done, the solid foundation counts for EVERYTHING!
With the welder, throw away the .030 wire that came with the machine and get some Lincoln .035 wire and use it. It will fit. You may have to get .035 tips from HF. Turn the voltage setting to high, the wire speed to 7 and PRACTICE ON SOME SCRAP! You are ready when the back of whatever you are welding has an evenly distributed line of dark blue discoloration the length of your weld. Get a book on mig welding or pay a welder his shop rate for an hour to give you some "hands on" pointers. Good luck! We all have to start somewhere, just don't give up!
#22
Registered User
If the amp ratings on those HF welders are honest you should be able to build it with that one. Will definitely need 035 wire of any brand to make it work with 1/4" though. Practice penetrating on scrap till you get results like Rob says and you should be able to do it with stock steel yourself. Cheaper and more satisfying than buying prefab.
These brackets below I built for mine are tied into the frame rails, though even the stock crossmember is surprisingly strong. I have completely maxed out the exact winch you have using this setup once, and come close many more times without issue.
http://a2.l3-images.myspacecdn.com/i...86a6f339/l.jpg
http://a1.l3-images.myspacecdn.com/i...2da09367/l.jpg
These brackets below I built for mine are tied into the frame rails, though even the stock crossmember is surprisingly strong. I have completely maxed out the exact winch you have using this setup once, and come close many more times without issue.
http://a2.l3-images.myspacecdn.com/i...86a6f339/l.jpg
http://a1.l3-images.myspacecdn.com/i...2da09367/l.jpg
#23
Registered User
Thread Starter
ok so on the way home im going to stop and get some .035 i just got some the other day but it was the stock stuff. .008mm thats what it came with, so ill run some .035 and see how that does, thanks for the info..
#24
Registered User
looking forward to seeing how this turns out, im looking at building one for mine too in the near future (actually my next project), great tips on here though. Post LOTS of pics!!!!!
#25
It has nothing to do with the wire diameter and everything to do with the welder, machine and person.
I could take my Pro Mig 135 and 0.023 wire and build a structurally sound bumper. Will I? No. I use my MM 251 and 0.030 wire and it will weld your face to the floor in a single pass. No need for 0.035 wire.
On your machine try flux core wire instead of using gas.
Practice. Practice. Practice. I learned to weld at a junior college one summer when I was bored. One of the best decisions I ever made.
Good luck.
:wabbit2:
I could take my Pro Mig 135 and 0.023 wire and build a structurally sound bumper. Will I? No. I use my MM 251 and 0.030 wire and it will weld your face to the floor in a single pass. No need for 0.035 wire.
On your machine try flux core wire instead of using gas.
Practice. Practice. Practice. I learned to weld at a junior college one summer when I was bored. One of the best decisions I ever made.
Good luck.
:wabbit2:
#26
Registered User
Thread Starter
i have never really took welding class, it has flex core in it right now, and i plan on practicing more, i will be having the whole thing gone over by someone that does weld a lot more then me with a 220 machine, i plan on adding more spots to hold and bracing so it is sound and wont pull off on me when i go to use it. it is just a learning process and i don't mind making mistakes and screwing up.. that's how u learn.
#27
Registered User
Yes, in skilled hands it's possible to do structural welding with 023 to some extent, but no need to make it more difficult than it has to be for beginners. I think you'll find it's easier to maintain a high amp arc with thicker wire. For reference - http://www.google.com/imgres?imgurl=...1t:429,r:8,s:0
BTW, aren't all the HFs 220 anyway? Good luck with it.
BTW, aren't all the HFs 220 anyway? Good luck with it.
#29
Registered User
Join Date: Apr 2010
Location: Floriduh & South Africa
Posts: 43
Likes: 0
Received 0 Likes
on
0 Posts
If you look on HF's website there is a forum. Many people have used the 90 amp welder with great success by switching to a name brand flux core wire. I suggested Lincoln because they sell it in the big box stores-you are not going to find miller wire at Home Depot. The main reason I told you to toss the HF wire to the dustbin was that the cheap chinese wire spatters all to hell and does not complete the circuit as well as the better wire. That machine will lay a bead with sufficient penetration, but you have to learn to do your part. Just easier to learn when your junk isn't fighting you every step of the way.
In Africa, we all used the cheap Chinese or Eastern bloc welders because that's all we had. The equivalent of $4000U.S. for a Miller 180 was just more than we could afford. Forget about premium shop migs-they ran $10,000 and up for Hobart, Lincoln and Miller 210's to 230's. Over there, we all learned on machines made in the same factories as the HF models you buy here.
In Africa, we all used the cheap Chinese or Eastern bloc welders because that's all we had. The equivalent of $4000U.S. for a Miller 180 was just more than we could afford. Forget about premium shop migs-they ran $10,000 and up for Hobart, Lincoln and Miller 210's to 230's. Over there, we all learned on machines made in the same factories as the HF models you buy here.
#33
If you bevel the edges so a weld can fill it in and lay flat it will look better and be stronger. If you just tack it together, it would be easy to drop it off at a welding shop and have them finish the welds. It wouldn't take long that way so it would not be a lot of $$.
#38
Registered User
Thread Starter
so now i have it all tacked up and ready got the welder to weld it all up. maybe by next weekend.
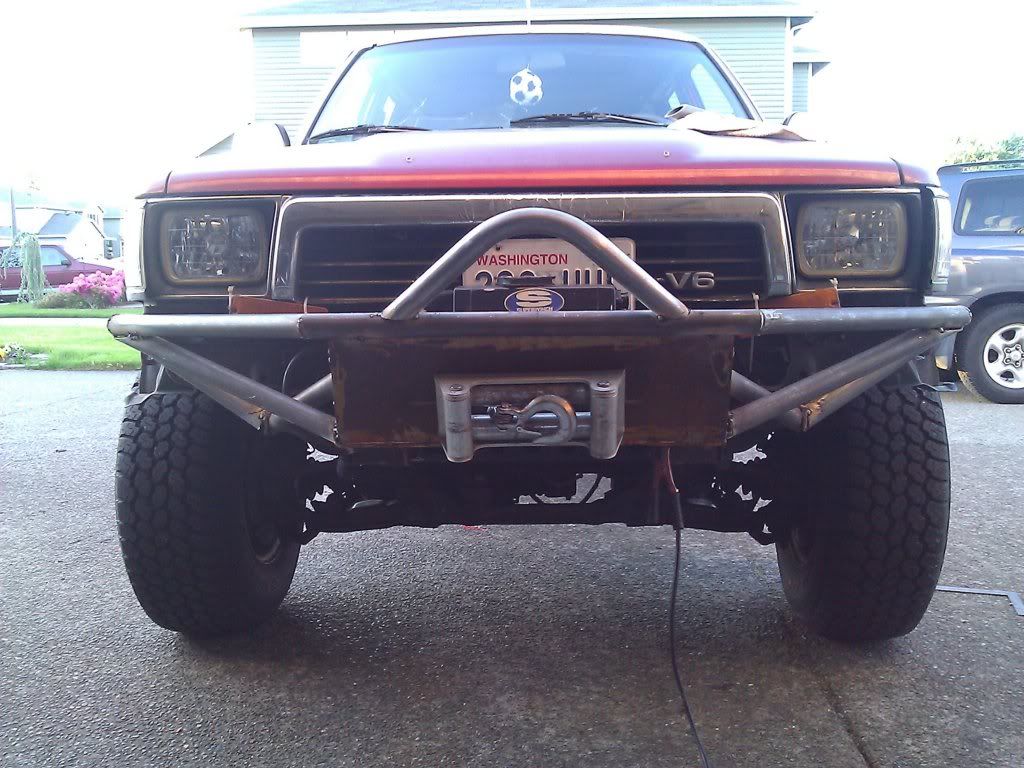

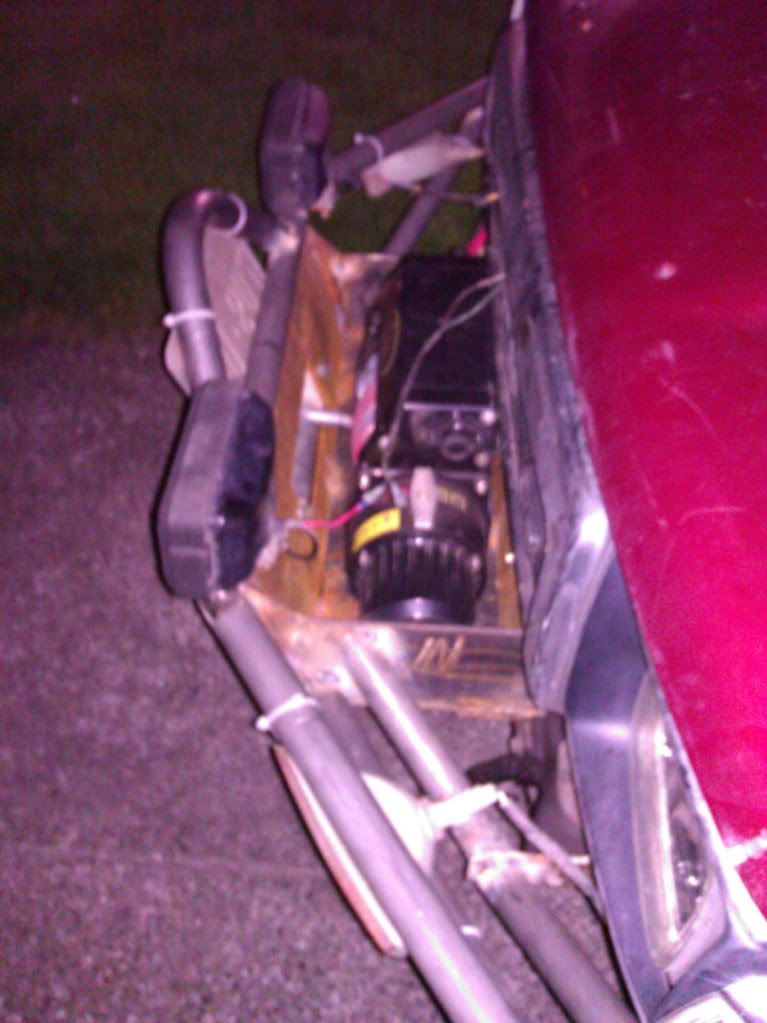
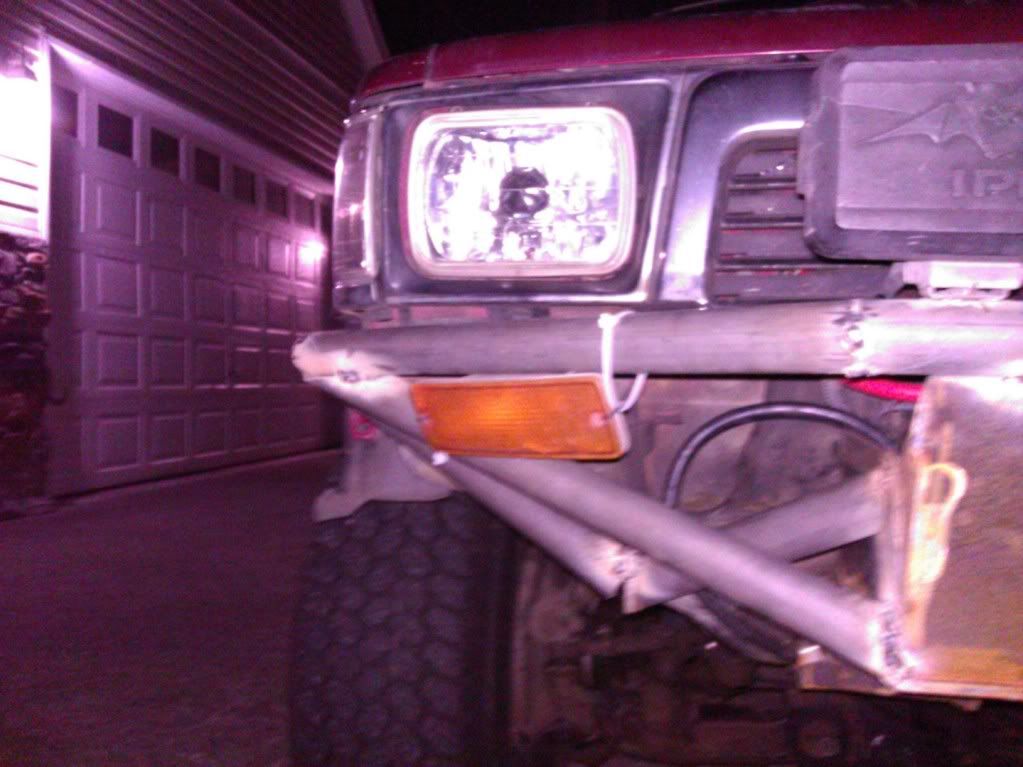
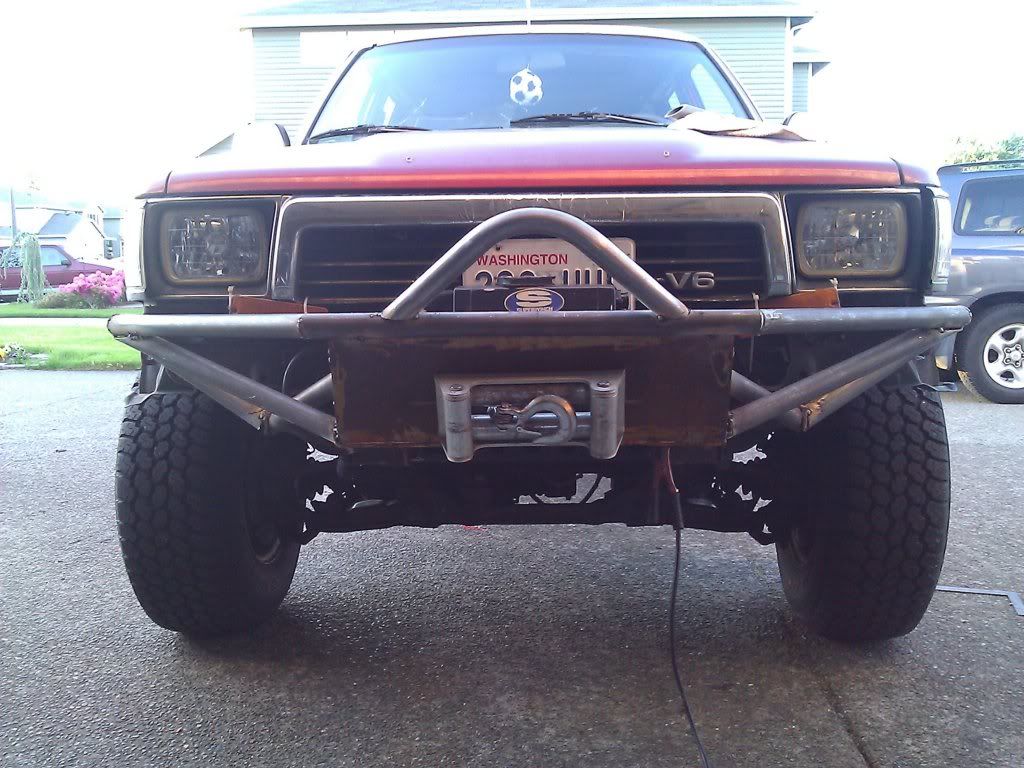

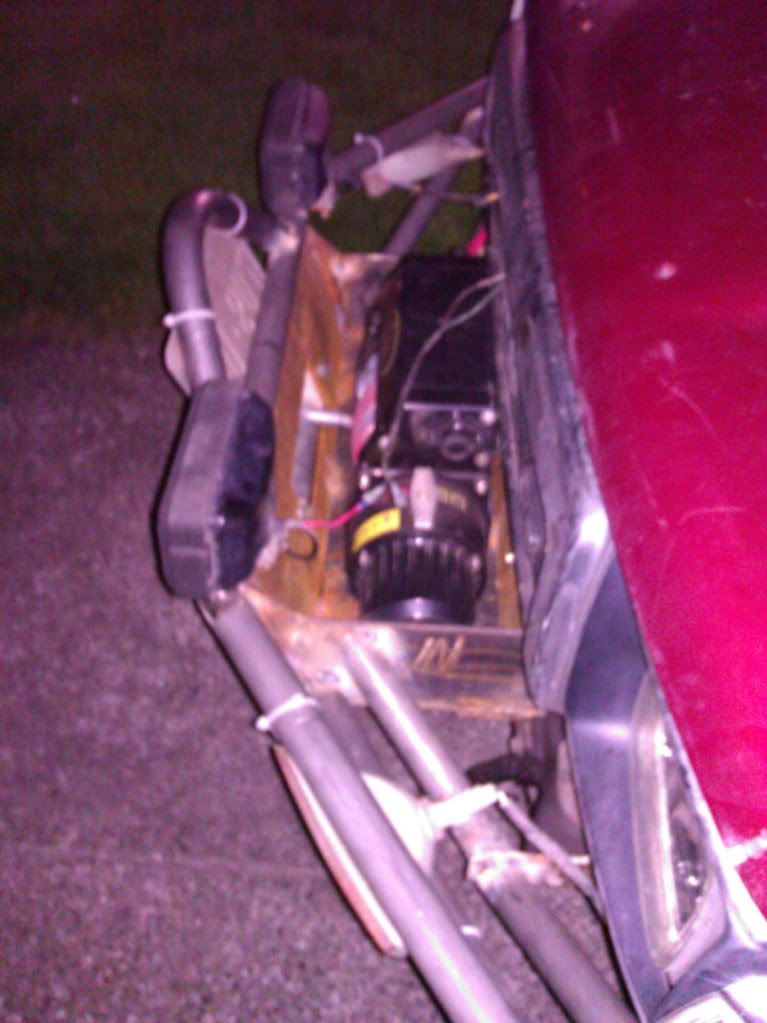
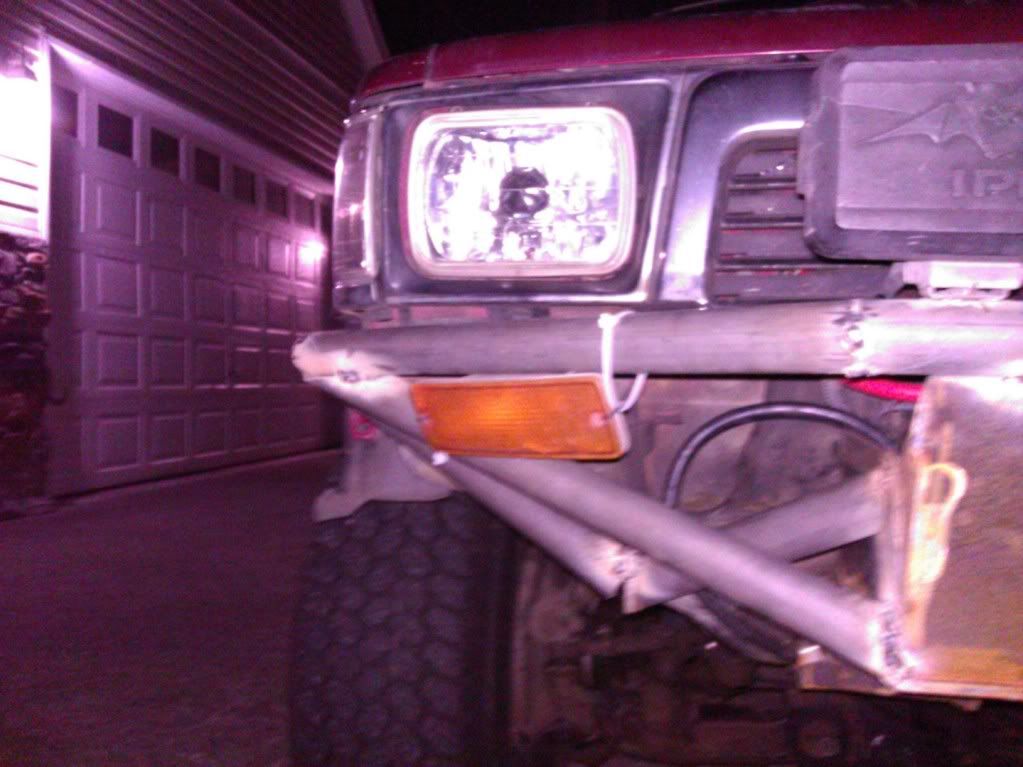
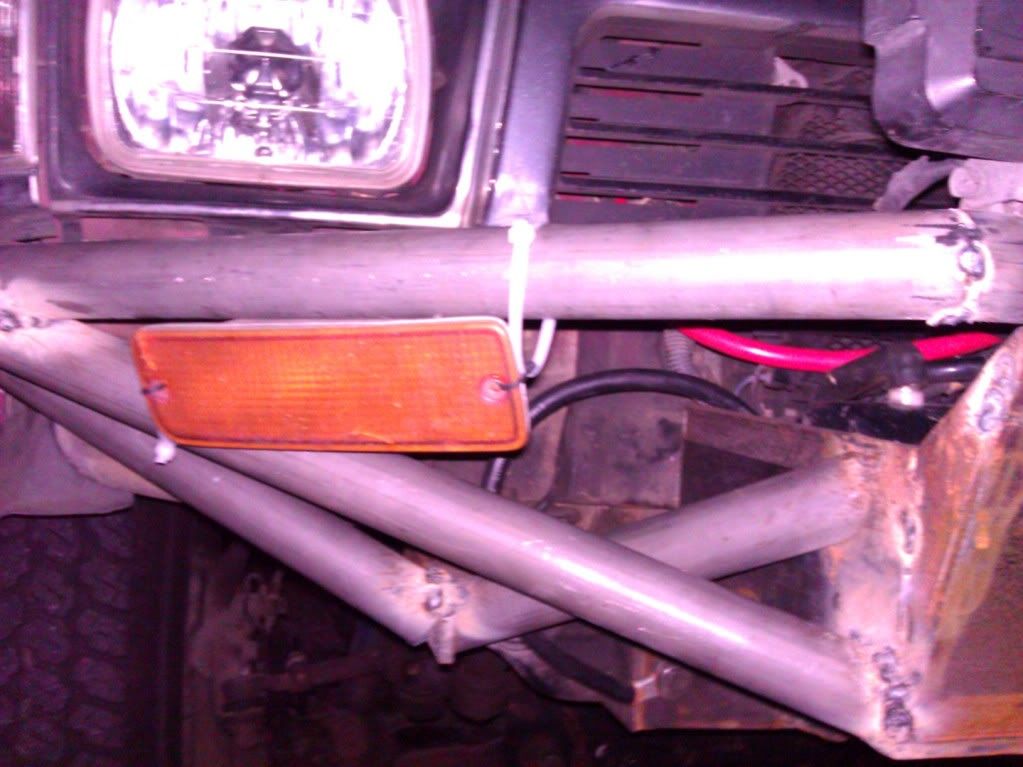
Last edited by justin_4runner; 06-03-2011 at 10:22 PM.
#39
Registered User
I like 0.030 vs the thinner stuff on our 140-120v... It's important to use a dedicated 20 amp outlet and the absolute shortest extension coord possible.
just my advice
just my advice